Synthetic mica, often referred to as fluorphlogopite, has revolutionized industries that demand materials combining beauty and resilience. Unlike natural mica, which is mined and can contain impurities, synthetic mica is manufactured in a highly controlled environment, resulting in a consistent and pure product.
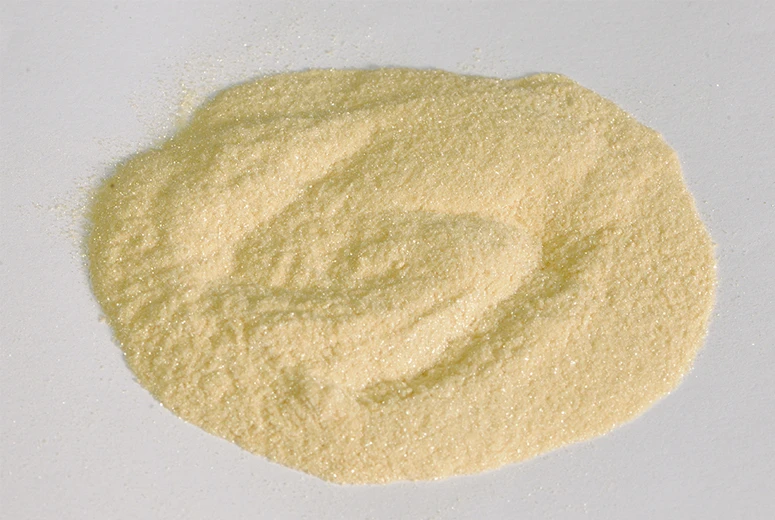
At its core,
synthetic mica is engineered from a blend of carefully chosen components. The primary ingredients include silica (SiO2), magnesium oxide (MgO), and potassium fluoroaluminate (KAlF3). These raw materials are fused at high temperatures—often exceeding 1300 degrees Celsius—to create a layered crystal structure similar to natural mica, yet superior in many performance aspects.
The process of creating synthetic mica begins with the melting of the raw materials together in exact proportions. This fusion results in a melt that, upon cooling, crystalizes into a sheet-like structure. This structure is then sliced into thin, even layers that can be polished to achieve a luxurious, glass-like finish. Each sheet of synthetic mica produced is free from the imperfections commonly found in its natural counterpart, such as cracks and inclusions, making it ideal for applications where uniformity and purity are paramount.

Markets such as cosmetics, electronics, and aerospace have increasingly leaned on synthetic mica for its unparalleled advantages. In cosmetics, synthetic mica is prized for its luminous effect without posing the safety risks associated with natural mica, which can sometimes contain heavy metals. The purity and controlled particle size distribution of synthetic mica make it a preferred choice for formulating high-end beauty products that offer an unparalleled glow and shimmer.
In the realm of electronics, synthetic mica's thermal stability and electrical insulation properties shine through. It can endure high temperatures and corrosive environments, essential for applications in capacitors and other high-performance electronic components. This reliability prolongs device life and enhances performance, contributing significantly to advancements in technologically driven industries.
what is synthetic mica made of
Furthermore, the aerospace sector benefits from synthetic mica’s lightweight yet robust characteristics. It is commonly used in composite materials and other components where both weight and performance are critical considerations. Its ability to withstand extreme temperatures and resist chemical attack makes it indispensable in environmental conditions that test the limits of human engineering.
Authenticity and trustworthiness of synthetic mica products are bolstered by stringent quality checks during production. Each batch is subject to rigorous testing to ensure consistency in chemical composition, thickness, and optical properties. Certifications accompanying most synthetic mica products verify that they meet international safety and quality standards, thus offering peace of mind to manufacturers and end-users alike regarding the product’s integrity.
One cannot overlook ecological considerations in synthetic mica production. The controlled manufacturing process not only ensures product uniformity but also reduces environmental impact compared to traditional mica mining. This eco-friendly aspect has elevated synthetic mica as a sustainable choice across industries, aligning with global movements toward greener manufacturing practices.
For professionals in industries that require materials exhibiting refined qualities, synthetic mica is an excellent choice. Its resilience, aesthetic appeal, and environmental benefits make it stand out as an exceptional material worthy of consideration for future innovations. As research and technology continue to advance, the potential applications of synthetic mica are likely to expand, promising even greater contributions to various sectors.